Did you know that businesses that utilize work order management software experience a 20% reduction in equipment downtime and material costs? This fact shows how crucial it is to manage work orders well. It's especially important for maintenance tasks across different industries.
What Is a Work Order?
A work order is a formal request for maintenance or repair tasks. It's key for smooth operations in many fields. This document lists the job details, like what needs to be done, where, what materials are needed, and how many workers are required.
There are different types of work orders, including:
- Maintenance Work Order: For regular upkeep and preventive maintenance tasks.
- Repair Work Order: For fixing current issues or breakdowns.
- Emergency Work Order: For urgent situations needing fast action.
- Project Work Order: For big projects that might take several tasks to complete.
Having these details in a work order helps teams talk better and stay accountable. It makes sure work is done well and keeps things running smoothly.
Type of Work Order | Description | Typical Use Cases |
Maintenance Work Order | Regular upkeep procedures to prevent future issues. | Scheduled inspections, HVAC maintenance |
Repair Work Order | Fixing existing equipment or system malfunctions. | Broken machinery, leaks |
Emergency Work Order | Immediate action required to address an urgent issue. | Pipes bursting, electrical failures |
Project Work Order | Long-term or ongoing projects needing multiple tasks. | Building renovations, system upgrades |
What Is Work Order Management?
Work order management is a way to keep track of maintenance tasks from start to finish. It helps you manage tasks like defining work scope, scheduling, and who does what. This method makes sure you use resources well and focus on urgent tasks.
At its core, work order management makes operations smoother, boosts efficiency, and ensures rules are followed. A reliable system lets companies stay competitive, improving productivity and asset life.
The Importance of Work Order Management
Work order management is key in today's fast-paced world. It keeps operations running smoothly and makes sure resources are used well. This leads to better asset performance and lower costs.
Having a strong work order management plan boosts productivity in many areas. When tasks are planned well, mistakes go down. This lowers risks and makes operations run smoother, from start to finish.
Following safety rules is also vital in work order management. A good system helps companies stick to safety laws. This keeps safety high and cuts down on risks. Being safe and running smoothly gives companies an edge in the market.
Work Order Management Process
The work order management process has several key stages. Each stage is important for making the workflow better. With these steps, you can make your operations smoother and more efficient.
Request Submission
The process starts with submitting a request. This can come from routine checks or urgent alerts. It highlights what needs maintenance or fixing.
Work Order Creation
After a request is made, the work order is created. It outlines the details and goals of the task. This makes sure everyone knows what to do.
Work Order Review
The work order is then reviewed carefully. This step checks if the request is complete and relevant. It helps filter out unnecessary requests and makes sure all needed info is there.
Prioritization
Tasks are then prioritized based on how urgent and important they are. This affects how resources are used next. Not all tasks are equally critical, so this step is key for managing tasks well.
Approval
After tasks are prioritized, they need approval from the right people. This ensures only tasks that are possible and needed move forward. It keeps the goals of the operation in line.
Scheduling
Scheduling sets the time and resources for the tasks. It organizes and assigns jobs to people, considering their availability and workload.
Assignment
Tasks are then given to specific team members. This makes sure everyone knows their role and reduces confusion during the task.
Execution
Execution is when tasks are done. It's important for everyone to follow safety rules and protocols here. This shows how crucial being precise is in the workflow.
Monitoring
Monitoring tasks as they are done helps ensure they're on track. Regular checks spot problems early on.
Completion
When tasks are finished, the work order is considered complete. This means all tasks listed in the work order are done, ready for the next step.
Quality Check
A quality check comes after completion. It makes sure all work meets the required standards. This keeps operations running smoothly and fixing any issues quickly.
Documentation
Documentation keeps track of all work done. It's useful for future tasks and helps understand past issues better. Accurate records help make the work order process more efficient.
Closure
The closure phase officially ends the work order once everything is checked and documented. This final step makes sure all is accounted for, ready for the next cycle.
Feedback Collection
Collecting feedback from those involved and stakeholders after the task is done. This encourages a culture of ongoing improvement and highlights areas that need work.
Reporting and Analysis
Reporting and analysis wrap up the work order process, as they turn it into useful insights. Looking at the data helps spot trends and guide decisions for better workflow optimization.
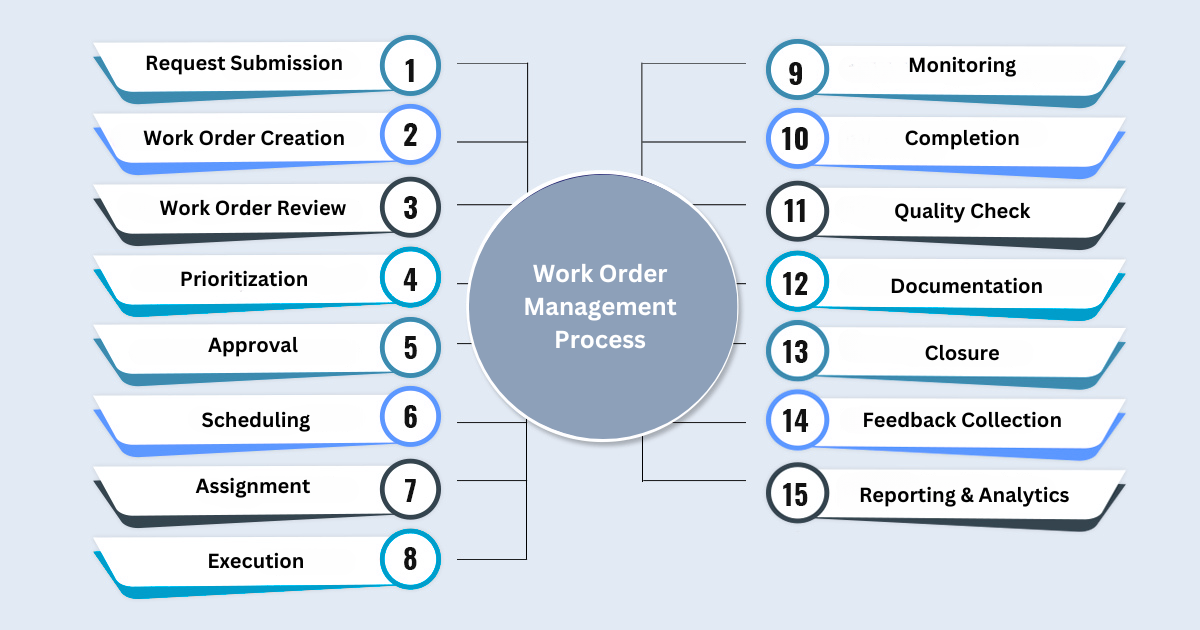
Benefits of Work Order Management
Using a strong work order management system has many advantages. It helps improve how things work and makes things more efficient. This is key for making the most of resources and improving service quality.
Improved Efficiency
Streamlining work order management boosts efficiency. Tasks get done faster when everything is organized and in order. This means more work gets done in less time.
Better Resource Allocation
Seeing what projects need and what resources are needed helps use assets better. This smart use cuts down on waste and makes the most of what you have. It's a big win for work order management.
Enhanced Communication
Good communication is key with work order management. It helps avoid mix-ups. Teams work better together, making sure everyone knows the project goals.
Increased Accountability
Clear roles in work orders make teams more responsible. Everyone knows what they're doing. This leads to fewer mistakes and more work getting done.
Streamlined Workflow
Organizing work orders makes workflows smoother. A clear plan helps avoid delays. This means problems get fixed faster.
Reduced Downtime
Regular maintenance cuts down on equipment downtime. Fixing issues early means things run better and on time. This is good for efficiency and keeping schedules.
Accurate Reporting
Work order systems give you timely, accurate reports. These reports help track progress and make better decisions. It's all about using data to improve operations.
Cost Control
Managing work orders well saves money. It avoids spending too much and keeps maintenance on track. This helps keep budgets under control.
Improved Customer Satisfaction
Finishing work orders on time means better service. Happy customers stay with you, which is key for success over time.
Enhanced Visibility
Seeing what's happening in projects helps make quick decisions. You can act fast if something goes wrong. This keeps things running smoothly.
Proactive Maintenance
A work order system encourages regular maintenance. This keeps equipment running well. It stops big problems before they start, saving money.
Better Compliance
Work orders help follow industry rules easily. Keeping accurate records and checking up regularly makes sure you're in compliance.
Data-Driven Decisions
Using data from work order systems helps make smart choices. Looking at past trends helps plan for the future better.
Scalability
A good work order system grows with your business. It handles more work without losing quality.
Improved Asset Management
Tracking work orders well improves managing assets. Knowing what assets are doing and their history helps plan better and use resources wisely.
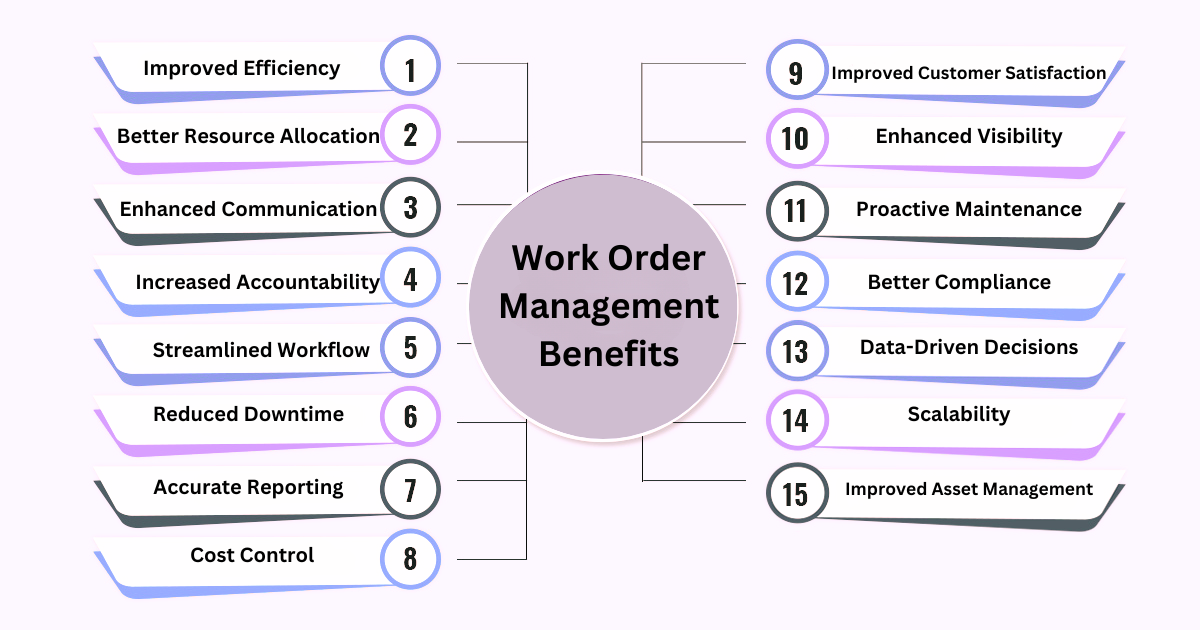
Work Order Management Best Practices
To make your work order management better, it's key to follow best practices. This means making strategies more effective and workflows smoother. Good communication makes sure your team knows what to do and can work together well.Â
Having standard ways of doing things improves consistency and quality. Putting tasks in order by their urgency and importance helps tackle the most critical ones first, keeping things running smoothly.
Clear Communication
Good communication among your team helps everyone know their role and the project's status. Using feedback helps everyone adapt and talk about any issues.
Standardized Procedures
Writing down how things should be done keeps quality high and processes consistent. It's key for making things run smoothly and making sure everyone knows what to do.
Prioritization
Putting tasks in order by their urgency and importance is key. This way, important tasks get done first, reducing downtime. Training your staff regularly keeps them up to date on these practices.
Detailed Documentation
Keeping detailed records of work orders and how things are done helps manage resources better and keeps everyone accountable. It also helps track how well your team is doing.
Regular Training
Training your team often keeps their skills sharp and up to date with new tech. Using the right software can make managing work orders easier and improve your workflows.
Utilize Technology
Choosing the right technology is key for managing work orders well. These tools help you keep an eye on things in real time and manage resources better, making your operations more efficient.
Performance Metrics
Tracking important metrics gives you insights into how well your operations are doing. This helps you see where you can get better, leading to ongoing improvements.
Feedback Mechanism
Having a way for feedback provides growth and improvement. Regular checks can spot areas that need work.
Preventive Maintenance
Doing maintenance before problems happen cuts down on unexpected issues and makes your assets last longer, saving your organization money.
Resource Management
Managing resources well is key to smooth operations. Checking how resources are used helps make sure everything is running at its best.
Regular Audits
Regular checks show how well your work order management is doing. They make sure you follow the rules and find areas to improve.
Collaborative Environment
Working together as a team makes executing work orders better and keeps everyone motivated and responsible.
Continuous Improvement
Always looking for ways to get better keeps your processes efficient, raises your performance, and keeps you following best practices for managing work orders.
Streamline Your Word Order Management with Kohezion
Are inefficient work order processes hampering your organization's productivity? With Kohezion, you can transform how you manage maintenance tasks, reducing downtime and boosting overall efficiency. Our robust work order management system allows you to seamlessly track and handle everything from routine upkeep to urgent repairs, ensuring that tasks are prioritized, assigned, and completed with precision.Â
Real-time mobile access and detailed analytics keep you ahead in today’s competitive market, offering unparalleled visibility and control over your operations. Streamline your workflows, enhance safety, and optimize resource allocation with Kohezion—empowering your team to achieve more with less effort.Â
Contact us today to make the switch today and experience the difference effective work order management can make!
Conclusion
Efficient work order management helps in maintaining smooth operations, maximizing productivity, and ensuring compliance with safety regulations. With a comprehensive system like Kohezion, organizations can streamline workflows, reduce downtime, and improve resource allocation.Â
Investing in effective work order management not only enhances communication and accountability but also drives continuous improvement, positioning your company for sustained success in a competitive landscape.
Start building with a free account
Frequently Asked Questions
Yes, most work order management systems can be integrated with other business tools like ERP systems, asset management software, and CRM systems, providing a seamless flow of information across the organization.
Preventive maintenance can be scheduled and tracked through work order management software, ensuring regular inspections and maintenance tasks are performed to prevent equipment failures and extend asset lifespan.
Industries such as manufacturing, healthcare, utilities, property management, and facility maintenance benefit significantly from effective work order management due to their reliance on regular maintenance and repairs.
Key features include task scheduling and prioritization, real-time updates, mobile access, integration capabilities, detailed reporting and analytics, and a user-friendly interface.